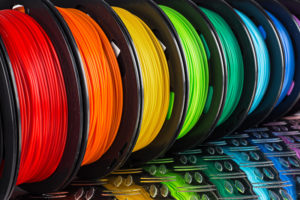
Filament Types for 3D Printers
Having trouble deciding which filament material to choose for your 3D project?
Filament types for 3d printers can often determine the quality and success of a print. Each material has different properties which will affect the final result. This sometimes makes choosing the correct material seem like a difficult task.
From rapid prototyping to small batch manufacturing or even functional parts, 3D printing is making what was once impossible, now possible. With high performance materials, 3D printing is now appealing to businesses worldwide who wish to reduce costs and speed up existing workflow processes.
The type of 3D filament you choose will depend on the desired result you hope to achieve. Each 3D printer has criteria that needs to be considered when choosing your filament. Mechanical resistance, chemical resistance, temperature resistance, flexibility and ease of use all play a part in a successful print result.
There is a wide choice of 3D filament materials available. As we have been in the industry for many years, we are happy to share with you some of the most commonly used 3D materials, their advantages and disadvantages and also technical specifications. We hope that this guide of filament types for 3D printers helps when purchasing your 3D filament.
PLA
PLA (Polylactic Acid) is the most commonly used filament type for 3D printers. This plastic filament is ideal for most prints that do not require mechanical resistance.
It is a filament which is easy to use and can be printed at a relatively low temperature, as a result this prevents warping and adhesion difficulties. It is also a material that does not produce toxic fumes when printing.
- Easy to print and low cost
- Environmentally friendly
- Glossy finish
- Odourless
- Heated bed is not required
- Wide range of colors
- Easy post-processing (sanding, painting etc.)
- Low Cost
- Strong and resistant
- Dimensional accuracy
- Good shelf life
- Low heat resistance
- Not flexible
- Sensitive to moisture
- Filament can get brittle and break
- Not suitable for prolonged outdoor use
- Functional prototypes
- Visual Prototypes
- Finished Products
- Tools
- Tensile modulus (T / F) : 2500 / 3000 Mpa
- Tensile strength: 48 Mpa
- Flexural strength: 103 Mpa
- Maximum elongation : 3.5%
- Impact strength : 4 kJ/m²
- Heat resistance : 55°C
- Extrusion temperature : 180 to 220°C
- Bed temperature : 60°C
- Print speed : 30 to 90mm/s
- Recommended ventilation : 100%
ABS
ABS (Acrylonitrile Butadiene Styrene) is a type of 3D printer filament which provides durability and resistance. When put under pressure, it will bend and deform before breaking. This makes it particularly suitable for printing screws, gears or mechanical systems that may be subjected to external forces.
ABS is a common polymer typically used in the industry for injection molding applications, this is why it will naturally retract more than other types of polymer. In 3D printing, retraction may cause bed adherence issues and warping.
Its high rigidity allows it to be used in the automotive industry, for household appliances or prints where resistance is important.
- Durable and rigid material
- Good mechanical, impact and wear resistance
- Resistant in most outdoor environments
- Easy post processing (sanding, painting etc.)
- Good heat resistance
- Low Cost
- Less stringing for a smoother finish
- Petroleum plastic, non biodegradable
- High risks of warping (strong bed adhesion is required)
- Needs heated bed or chamber
- Produces a pungent odour and VOCs while printing
- Parts tend to shrink leading to dimensional inaccuracy
- Functional prototypes
- Visual prototypes
- Finished Products
- Tools
- Tensile modulus (T / F) : 1700 / 2300 Mpa
- Tensile strength: 35 Mpa
- Flexural strength: 60 Mpa
- Maximum elongation : 4 %
- Impact strength : 11 kJ/m²
- Heat resistance : 85°C
- Extrusion temperature : 230 to 250°C
- Bed temperature : 80 TO 100°C
- Print speed : 30 to 70mm/s
- Recommended ventilation : 5%
ABS CARBON
ABS carbon is a 3D filament type that has been specifically designed for 3D printers. It is made from a blend of Acrylonitrile Butadiene Styrene (ABS) reinforced with carbon fibers.
It provides excellent printing Properties that prevent the nozzle from clotting and damaging the printer. It provides 35% more tensile modulus than standard ABS and it is compatible with the majority of 3D printers with heated beds.
- Durable and rigid material
- Good mechanical, impact and wear resistance
- Dimensional stability
- Easy post processing (sanding, painting etc.)
- Less wear on the 3D printer
- Heated bed required
- Prone to warping
- Functional prototypes
- Finished Products
- Tools
- Tensile modulus (T / F) : 2700 Mpa
- Flexural Modulus: 2700 Mpa
- Maximum elongation : 10 %
- Impact strength : 11 kJ/m²
- Softening Temperature : 101°C
- Extrusion temperature : 250 to 270°C
- Bed temperature : 90 to 110°C
- Print speed : 30 to 70mm/s
ASA
ASA (acrylonitrile styrene acrylate) is a 3D filament that is derived from ABS and is an excellent alternative to ABS if needed. It offers higher UV heat resistance and fantastic mechanical properties making it perfect for everyday or technical prints. It is also suitable for outdoor use.
Similar to ABS, this material has a smooth finish. It can be successfully used in the automotive industry and bodywork printing due to high heat resistance.
- Durable material
- Good mechanical, impact and wear resistance
- Resistant in outdoor environments, UV resistant
- Easy to post-processing (sanding, painting etc.)
- Good heat resistance
- Ideal material for industry
- High resolution
- High glass transition temperature
- Petroleum plastic, non biodegradable
- Expensive
- Requires higher extruder temperatures
- Requires ventilation due to potentially dangerous fumes
- Outdoor Prototypes
- Functional Prototypes
- Finished Products
- Tensile modulus (T / F) : 2000 / 1900 Mpa
- Tensile strength: 44 Mpa
- Flexural strength: 72 Mpa
- Maximum elongation : 5 %
- Impact strength : 9 kJ/m²
- Heat resistance : 85°C
- Extrusion temperature : 240 to 260°C
- Bed temperature : 80°C
- Print speed : 30 – 70mm/s
- Recommended ventilation : 5%
HIPS
HIPS (High Impact Polystyrene) is a light yet solid material. It is impact resistant with high detail, this makes it suitable for many projects.
It is also used as a support material with double extrusion with materials such as ABS or ASA. This material easily dissolves in D-limonene (lemon-based solvent) after a few hours.
- Impact and water resistant
- Lightweight
- Good dimensional stability
- Easy to treat (sanding, painting etc.)
- Nice matt and smooth appearance
- Can be used as support material with ABS
- Less warping
- Ideal material for industry
- High resolution (for detailed prints)
- Low cost
- Dissolvable in d-Limonene
- UV sensitive
- Non biodegradable
- Heated bed required
- Heated chamber recommended
- High printing temperature
- Ventilation required
- Functional Prototypes
- Visual Prototypes
- Product packaging, Toys
- Tensile modulus (T / F) : 1550 /1500 Mpa
- Tensile strength: 22 Mpa
- Flexural strength: 35 Mpa
- Maximum elongation : 20 %
- Impact strength : 15 kJ/m²
- Heat resistance : 85°C
- Extrusion temperature : 230 to 250°C
- Bed temperature : 70 to 110°C
- Print speed : 40 to 80mm/s
- Recommended ventilation : 0 – 10 %
PETG
PET (Polyethylene terephthalate) filament is a polyester plastic used for bottles, packaging and many of our everyday products. It is a strong filament that results in a solid print.
This common material has a glossy appearance and has been FDA approved. It is also waterproof making it suitable for food packaging.
- Easy to print
- High chemical resistance
- BPA Free: Low shrinkage
- Low moisture absorption
- Odourless
- No enclosure required
- Glossy smooth finish
- Adheres well to the bed with negligible warping
- Requires precise configuration
- Little flexibility, rigid material
- Lower scratch resistance
- Poor bridging properties
- Possible stringing
- Functional Prototypes
- Visual Prototypes
- Tools
- Finished Products
- Tensile modulus (T / F) : 1600 /2000 Mpa
- Tensile strength: 45 Mpa
- Flexural strength: 65 Mpa
- Maximum elongation : 5 %
- Impact strength : 8 kJ/m²
- Heat resistance : 80 °C
- Extrusion temperature : 230 to 260°C
- Bed temperature : 70°C
- Print speed : 30 to 90mm/s
- Recommended ventilation : 0 – 50 %
Polycarbonate
Polycarbonate (PC) filament is the strongest standard thermoplastic material. This plastic is used for car headlights, glasses, home appliances etc. It has high mechanical resistance which is perfect for high temperatures (up to 140°). This 3D filament material is suitable for automotive, aerospace or industry manufacturers.
- Excellent mechanical and impact resistance
- Good dimensional stability
- Suitable for printing moulds
- High heat resistance
- Naturally transparent
- Flexible
- High-performance 3D printer required: mandatory closed chamber, 280°C +
- Toxic VOCs
- Prone to warping
- Possible oozing while printing
- Absorbs air moisture which sometimes causes print defects
- Functional Prototypes
- Tools
- Finished Products
- Tensile modulus (T / F) : 2000 /2300 Mpa
- Tensile strength: 60 /63 Mpa
- Flexural strength: 95 / 100 Mpa
- Maximum elongation : 12 % / 3%
- Impact strength : 4 kJ/m² / 15 kJ/m²
- Heat resistance : 110 °C
- Extrusion temperature : 260 to 300°C
- Bed temperature : > 110°C
- Print speed : 30 to 60mm/s
NYLON
Nylon 3D filament is highly resistant to chemicals and extreme temperatures and is often used for small parts and in the food industry. There are a number of different types of Nylon filament and we have outlined the pros and cons of the most popular types below:
PA6
- Extremely strong filament
- Excellent mechanical, abrasion and impact resistance
- Resistant in harsh climatic conditions
- Good dimensional stability
- Little warping, suitable for printing moulds
- Strong and partially flexible
- No unpleasant odour while printing
- Adhesion difficulties
- Poor dimensional stability
- Prone to warping
- Air-tight storage required to prevent water absorption
- Filaments that are not dried properly may cause printing defects
- Functional Prototypes
- Tools
- Tensile modulus (T / F) : 850 /1900 Mpa
- Tensile strength: 37 Mpa
- Flexural strength: 35 Mpa
- Maximum elongation : > 20 %
- Impact strength : 8 kJ/m²
- Heat resistance : 70 °C
- Extrusion temperature : 240 to 260°C
- Bed temperature : 60°C
- Print speed : 30 to 70mm/s
- Recommended ventilation: 40%
PA66
- Higher mechanical resistance than PA6
- Excellent climatic resistance
- Durable
- Less sensitive to moisture than the PA6
- Strong and partially flexible
- Odourless
- Non-biodegradable materials
- Prone to Warping
- Functional Prototypes
- Tools
- Tensile modulus (T / F) : 2000 / 2100 Mpa
- Tensile strength: 42 Mpa
- Flexural strength: 40 Mpa
- Maximum elongation : 10 %
- Impact strength : 5 kJ/m²
- Heat resistance : 90 °C
- Extrusion temperature : 240 to 260°C
- Bed temperature : 60°C
- Print speed : 30 to 70mm/s
- Recommended ventilation: 40%
PA 11/12
- Impact and abrasion resistant
- Greater flexibility
- Moisture resistant
- Dimensional stability
- Resists temperatures as low as -40°C
- UV resistant (PA11 only)
- Odourless
- Non-biodegradable materials
- Prone to Warping
- Functional Prototypes
- Tools
- Tensile modulus (T / F) : 600 / 1200 Mpa
- Tensile strength: 25 Mpa
- Flexural strength: 22 Mpa
- Maximum elongation : >50 %
- Impact strength : 12 kJ/m²
- Heat resistance : 90 °C
- Extrusion temperature : 240 to 260°C
- Bed temperature : 60°C
- Print speed : 30 to 70mm/s
- Recommended ventilation: 40%
Polypropylene
Polypropylene 3D filament is a versatile, semi-rigid and lightweight material that is commonly used for food packaging and technical parts. Printed parts are both moisture and heat resistant.
The disadvantage of this 3D printing material is that printed parts may warp after cooling which makes printing more challenging.
- Durable filament
- FDA approved
- Resistant to chemicals and friction
- Excellent electrical insulation
- Good heat resistance
- Smooth surface
- Mandatory slow print speed
- Heavy warping
- Low strength
- Difficult to adhere to bed and other adhesives
- Expensive
- Functional Prototypes
- Visual Prototypes
- Tools
- Tensile modulus (T / F) : 230 Mpa
- Tensile strength: 9 Mpa
- Flexural strength: 13 Mpa
- Maximum elongation : 200 %
- Impact strength : 34 kJ/m²
- Heat resistance : 100 °C
- Extrusion temperature : 200 to 215°C
- Bed temperature : 80 to 100°C
- Print speed : 40 to 120mm/s
- Recommended ventilation: 20%
TPU
Flexible and semi-flexible TPE / TPU (thermoplastic elastomers) filaments are often used as technical plastics or as a replacement for rigid rubbers.
This material allows you to print objects that can be stretched or folded while retaining their original shape and elasticity. The material is ideal for printing soles, insoles, straps, or any other object that requires flexible properties. It is compatible with most FDM 3D printers.
- Flexible and soft
- Excellent vibration dampening
- Long shelf life
- Returns to original shape after deformation
- Wear and tear resistant
- Works in combination with PVA (soluble support material)
- Requires a heating plate
- Mandatory slow print speed
- Difficult to print
- Poor bridging Properties
- Possibility of blobs and stringing
- May not work well on Bowden extruders
- Functional Prototypes
- Tools
- Tensile modulus (T / F) : 25 / 80 Mpa
- Tensile strength: 8 Mpa
- Flexural strength: 4 Mpa
- Maximum elongation : > 500 %
- Impact strength : 34 kJ/m²
- Heat resistance : 80 °C
- Extrusion temperature : 190 to 240°C
- Bed temperature : 70 to 100°C
- Print speed : 30 to 60mm/s
- Recommended ventilation: 20%
PVA
PVA is a 3D filament material which is known for its ability to dissolve in water. This makes it perfect for complex prints.
PVA is also suitable as a print material for quick prototypes.
- Water dissolvable support material
- Odourless
- Simple to print
- Does not require a heated bed
- Perfect support for printing complex parts
- Airtight storage containers required
- Fragile material
- Chance of clogging if the nozzle is left hot while not extruding
- Expensive
- Functional Prototypes
- Tools
- Tensile modulus (T / F) : 3860 Mpa
- Tensile strength: 78 Mpa
- Maximum elongation : 9.9 %
- Impact strength : 1.6 kJ/m²
- Bed temperature : 70 to 100°C
- Print speed : 30 to 60mm/s
- Melting Temperature : 163°C
- Melt Mass Flow: 17-21 g / 10 mins
PAEK FAMILY
The PAEK (Polyaryletherketone) 3D filament family includes two main types of material: PEEK (Polyetheretherketone) and PEKK (Polyetherketetonketone). These thermoplastic, semi-crystalline polymers are the best performing plastics available in 3D printing. With excellent thermomechanical and chemical properties, the PAEK family of 3D filament is the solution used in the aerospace industry (light / fireproof / high mechanical and heat resistance) and surgical (chemically).
It is important to note that this filament cannot be used on most desktop 3D printers.
PEEK
- High mechanical resistance
- Lightweight (compared to metal)
- Resistant in high temperatures
- Chemical resistance
- Dimensional stability
- Fire-resistant
- UV resistant
- Sterilization possible
- Expensive and complex material to print
- Moisture sensitive (before printing)
- Variable crystallization rate
- Functional Prototypes
- Tools
- Tensile modulus (T / F) : 3900 Mpa
- Tensile strength: 100 Mpa
- Flexural strength: 130 Mpa
- Maximum elongation : 30 %
- Impact strength : 4.5 kJ/m²
- Heat resistance: 240°C
- Extrusion temperature : 375 to 450°C
- Bed temperature: 70 to 110°C
- Print speed : 40 to 80mm/s
- Recommended ventilation : 0 – 10°C
PEKK
- Mechanical resistance
- Lightweight (compared to metal)
- Resistant in high temperatures
- Chemical resistance
- Dimensional stability
- Fire-resistant
- UV resistant
- Sterilization possible
- Expensive and complex material to print
- Moisture sensitive (before printing)
- Variable crystallization rate
- Functional Prototypes
- Tools
- Tensile modulus (T / F) : 2900 Mpa
- Tensile strength: 850 Mpa
- Flexural strength: 100 Mpa
- Maximum elongation : 8 %
- Impact strength : 5 kJ/m²
- Heat resistance: 260°C
- Extrusion temperature : 350 to 420°C
- Bed temperature: 80°C
- Print speed : 20 – 40 to 80mm/s
- Recommended ventilation : 0 – 10°C
Follow us on LinkedIn to stay AM informed!
Disclaimer: Due to the vast number of materials available and new filaments coming to market, we will be updating this article regularly.